Poultry and Livestock Manure Storage: Management and Safety
ID
442-308 (BSE-360P)
EXPERT REVIEWED
Introduction
Storing manure is a common practice on farms and for those who keep animals. A well-designed manure storage facility must also be well managed in order to prevent environmental concerns from developing. In most cases, manure storages are used when cold weather, wet conditions, and/or a lack of time do not allow field application. To get the most benefit out of the manure, good management practices and observation of safety practices that minimize manure hazards on the farm are important. This publication provides guidelines for good management and safety practices for manure storage.
Managing of Manure Storage
To maximize environmental, agronomic, and economic benefits on the farm, it’s crucial to handle manure storage facilities properly. When manure management is inadequate, it can lead to inefficiencies in farming operations—such as delays in land preparation and planting, resulting in reduced crop yields. Additionally, poorly managed manure storage areas can emit unpleasant odors that might bother your neighbors. Key management considerations for manure storage structures involve regular manure removal, monitoring the storage structure’s integrity, and paying attention to appearance and aesthetics.
Manure Removal
Removing manure from storage in a timely manner is an important aspect of the overall manure management on the farm. How fast manure is removed from storage and moved to the point of use depends on the (1) size of equipment, e.g., front-end loaders for handling solid manure; (2) volume of hauling tanks; (3) pump sizes; and (4) condition of the equipment. The volume of the hauling equipment and the distance manure is hauled will determine the time it takes to empty a manure storage tank. Consider all these factors when planning manure application in order to improve the operation’s time management and efficiency. Make sure the equipment used for removing manure from storage is serviced and in good condition to avoid breakdowns that can cause delays during manure removal.
Manure should be used at locations, times, rates, and volumes that will ensure maximum nutrient use and avoid environmental pollution. The Natural Resources Conservation Service’s (NRCS) Virginia Conservation Practice Standards: Nutrient Management (code 590) and Virginia Conservation Practice Standards: Waste Utilization (code 633) provide guidelines on how to utilize manure efficiently.
A manure storage structure should never leak or overflow. If properly designed, constructed, located (see Selection and Location of Poultry and Livestock Manure Storage, VCE publication 442-307), and managed, no discharge should occur. Because the discharge from manure storage contains nutrients, organic matter, and perhaps pathogens, it may cause pollution if it ends up in groundwater or surface water. Any discharge will most likely violate local, state, or federal regulations, resulting in fines or other penalties. Thus, it is critical to remove manure from storage promptly and at the planned time in order to prevent discharges. Some discharge problems may occur when a producer is unable to prepare adequately for manure application.
Monitoring Manure Storages
Monitoring the condition of manure storage structures is necessary to ensure they are performing as expected. Monitoring manure storages indicates good management and stewardship. Activities to consider include: periodic inspections, pumping activities, record keeping, manure nutrient content, and appearance and aesthetics.
Periodic Inspections
A manure storage structure should be inspected periodically to detect any potential problems and avoid negative environmental impacts from manure overflow. Develop a regular inspection schedule for each component. Inspection frequency will depend on size and complexity of the system, mechanical devices such as pumps and switches, proximity to a water source, type of storage structure, and occurrence of rainfall. Make a checklist of items to be inspected and include times and dates of inspections. Items on the checklist will depend on the type of storage. Some examples of items to include on the checklist can be found in the section below, but a detailed list can be derived from the NCRS technical guide Virginia Operation and Maintenance Requirements: Waste Storage Facility (code 313).
Liquid or slurry level: For liquid/slurry storage structures, ensure that you have adequate freeboard and that the liquid-level marker (staff gauge) is visible. The staff gauge should be graduated to indicate how much storage volume is available. A properly designed structure has the capacity to handle manure from a specific number of animals for a given time period. If a pit designed for 120 days of storage receives designated manure amounts but does not fill to the designed level, the pit may be leaking. Evaporation from uncovered liquid storages should be minimal during the late fall, winter, and early spring. During these times, if additional liquids have to be added so that a pit can be agitated and pumped, it may be leaking. If there is more evaporation than rainfall in your area, additional liquids may be needed to dilute manure for pumping due to evaporation losses during the warm months. Monitoring wells installed around the pond upslope and downslope would be required to confirm seepage.
Earthen storage structures: Check the interior lining for erosion and signs of damage to the berm/dam; check for indications of seepage at the toe of the berm; check for damp, soft, or slumping areas on berms; and check for seepage around pipes through the berm. Inspect the liner for signs of damage, erosion, or other factors that may compromise its integrity.
Concrete or steel tanks: Check for cracks or structural damage, leakage, or wet spots around the base; ensure that an escape ladder is available and in working condition. Inspect and maintain positive drainage away from the facility.
Pumping Activities
Discharges and spills sometimes occur when manure is being pumped. The spills may be caused by burst or ruptured piping, leaking joints, or overfilled hauling equipment. Thus, pumping activities should be monitored closely − especially in the startup phase − to minimize spillage. Continuous irrigation pumping systems can be equipped with automatic shutoff devices (which usually sense pressure) to minimize the risk of discharge in the event of system failure. Maintain all pumps, agitators, piping, valves, and other mechanical and electrical equipment in good operating condition by following the manufacturers’ recommendations.
Record Keeping
Records kept on the manure storage structures can help in overall maintenance and management. Keeping records is also an indication of responsible operations and good stewardship. Record all observations made during routine inspections. Record levels of manure in storage and use them to determine the effects of excessive rainfall on the volume of your structure. The manure levels will also provide a rate of accumulation that will help schedule future pumping activities. When the manure storage is pumped out, record the volume of manure removed and the locations where manure is spread.
Manure Nutrient Content
Collect manure samples from the storage structure and send them to a lab for nutrient analysis every time manure is pumped out. The lab reports will be useful in nutrient-management plan development.
Appearance and Aesthetics
Appearance and aesthetics are major factors in the general public’s perception of your facility. Therefore, it is very important that aesthetics and appearance be given priority for the overall benefit and viability of animal agriculture. Remove any medical consumables floating in the manure and mortalities or afterbirth that may have been dumped in the storage structure.
Landscape: A clean, well-landscaped production area will project a positive image for the operation. Do not leave any debris or litter lying around the storage structure or the farm in general. Typical items of concern include leftover construction debris, old unused vehicles, worn-out equipment, rusted barn equipment, loose roofing panels, worn-out ventilation curtains, etc.
Mowing: Maintaining front-yard-quality lawns around manure storage facilities provides a very powerful first impression of responsibility (figure 1). Routine inspections for seepage, rodent burrowing, erosion, or other damage to the storage structure are more easily conducted if the areas have been mowed.
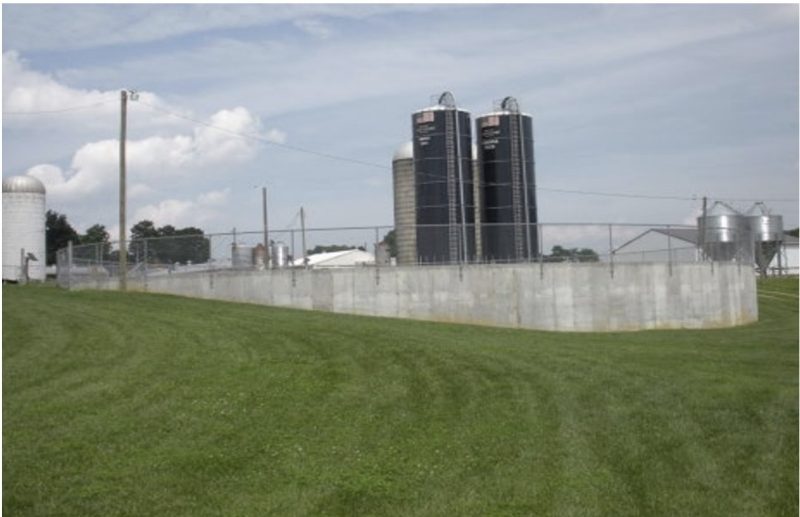
Surface water: Develop a surface-water management plan so that no damage due to erosion occurs, such as unwanted ditches or washed-out culverts or waterways.
Manure Storage Safety
Manure can be stored as a solid, semisolid, or liquid, depending on the dry matter content. No matter how manure is stored, safety is a critical issue. The greatest safety concern in manure storage is the gas produced as a result of manure decomposition when in storage. Liquid and semiliquid manure storages that are handled by moving manure through pumping, mixing, or spreading can release large amounts of dangerous gases when compared to other forms of manure storage. The gases of concern are hydrogen sulfide (H2S), ammonia (NH3), carbon dioxide (CO2), and methane (CH4) (see table 1).
In general, belowground storage facilities or pits are more hazardous than aboveground structures; and systems that are covered by lids, caps, or slotted floors are more hazardous than uncovered systems. Thus, the most dangerous storage facilities are pits located within buildings or directly beneath livestock structures because of the lack of adequate ventilation and the accumulation of hazardous gases. Pump-out pits can also be very hazardous.
Fatalities from manure gases have occurred when the effects of toxic manure gases are compounded by oxygen displacement in a space (asphyxia) and/or the occurrence of explosions of combustible gases. A summary of the characteristics of these gases and how they can affect you are presented in table 1. The maximum safe time-weighted average gas concentration, or threshold limit values (TLV-TWA) for human exposure for an eight-hour workday and 40-hour workweek have been established by the American Conference of Government Industrial Hygienists (ACGIH) and are also presented in table 1. The concentrations are temperature-dependent, and the values present are for 77 °F.
Manage manure pits and tanks (whether covered or not) as “confined spaces.” A confined space is a space that has limited means of entry or exit, is large enough for a person to enter, and is not designed for continuous human occupancy. Death from asphyxiation and/or the toxic effects of manure-pit gases can occur when someone enters a manure pit. Therefore, post warning signs at all confined-space locations that alert people to “KEEP OUT.” The signs should also contain the potential dangers of entering the confined space. To keep these areas safe, follow the tips below.
Safety Tips
- Observe safety precautions when entering manure pits. It is easy to be overcome by manure gases. Even if a manure pit has been emptied, it may still contain high concentrations of manure gases or there may not be enough oxygen present to support life. In an emergency situation, the best thing to do is to ventilate the pit or area and call rescue personnel with the proper equipment.
- Get training on how to use and maintain safety equipment such as respirators, safety harnesses and lifelines, and self-contained breathing apparatus (SCBA) equipment (see Respiratory Protection in Agriculture, VCE publication 442-601).
- Do not enter manure sumps, pits, storage tanks, or spreader tanks without appropriate safety apparatus. No tool, pump part, or farm chore is worth the cost of a human life.
- If you have to enter a manure pit or tank, you MUST wear an air-supplying respirator that you have been trained to use and maintain. Use confined-space entry procedures by wearing a safety harness and lifeline connected to a stationary object outside the pit. Make sure there are at least two people equipped with their
Gas | Symbol | Possible effect and characteristics |
---|---|---|
Ammonia | NH3 |
Corrosive, toxic, and odorous: may cause severe damage to the eyes, throat, and lungs when it combines with moisture in the mucous membranes to form a caustic solution (alkaline base) that causes burns. Ammonia has a threshold limit value (TLV-TWA) of 25 ppm. |
Carbon dioxide |
CO2 | Asphyxiant: nontoxic gas that will displace oxygen in a space, asphyxiating humans and animals. It is both colorless and odorless. Carbon dioxide can only be identified using detection equipment. Carbon dioxide gas (TLV-TWA) is 5,000 ppm. |
Hydrogen sulfide |
H2S |
Toxic and odorous: most hazardous manure gas. Common in facilities with closed manure storages. A colorless gas and heavier than air, it starts accumulating near the bottom of a tank. Produced under anaerobic conditions. Has a rotten egg smell and can be detected at very low concentrations. Hydrogen sulfide gas (TLV-TWA) is 10 ppm. |
Methane | CH4 | Asphyxiant, explosive: highly flammable and explosive. Itis odorless and colorless and impossible to measure without detectors. Methane is lighter than air and rises easily from storage areas. When produced in large quantities, methane will displace air and can cause asphyxiation. Methane (TLV-TWA) is 1,000 ppm. |
- Uncovered storages at ground level, such as manure ponds or lagoons, should be fenced to prevent access by livestock and unauthorized people. If possible, use reflective tape on posts and fencing to increase visibility.
- Manure storages located under floors should have adequate ventilation, especially where livestock are kept. Keep people and livestock out of confinement when a manure pit is being agitated for emptying and there is not adequate ventilation. Before agitating, take steps to ensure the welfare of the animals and the people working in the area. Remove all people and animals. If animals cannot be removed, maximize ventilation and agitate slurry very slowly at first. Monitor the condition of the animals. If the animals act in a restless, disturbed, or abnormal manner, stop the agitation immediately and ventilate the area.
- Provide permanent ladders both inside and outside aboveground storage tanks to provide access to manure storage. The outside ladder should have a locking mechanism to keep people away from the tank. Do not leave temporary-access ladders leaning against aboveground tanks.
- When someone collapses in a pit, gases are so concentrated that it would be suicidal for anyone else to enter without an SCBA. The only reasonable immediate action is to ventilate the storage area and notify rescue personnel who can bring the proper equipment. Barn fans and silo blowers can be activated to provide ventilation, but do not lower fans into the pit because this could cause a methane explosion. Properly sign the area (figure 2).
- Liquid manure can become crusty on top and look solid enough to walk on. Post warning signs (figure 2) about the unstable walking surface to prevent engulfment and drowning: “Danger: Surface is not solid.”
- Install and maintain a fence around the area of farm ponds and manure lagoons. An adequate fence will keep unsupervised visitors away and prevent drowning.

- As a safe work practice, remove all unnecessary personnel from around a manure pit before agitating or pumping. Maximize ventilation in the area using fans and blowers. Be careful not to place the equipment too close to the manure – an electric spark or open flame could ignite flammable methane gas and cause an explosion. Start the agitation slowly in order to control potential gas release. Never enter a manure pit during or immediately after agitating or pumping.
- If the storage structure is damaged and there is a danger of imminent failure, empty the storage facility immediately. Seek the services of a qualified engineer to assess the situation.
Emergency Plans
An emergency plan provides a list of cleanup and containment practices to use in case of an overflow, breach, leak, fire, or need for emergency land application. It also contains a list of phone numbers for appropriate first responders: fire departments, police, hospitals, and other emergency contacts. Your local county Extension office or soil and water conservation district can help you prepare an emergency plan.
Small manure spills (less than 10 gallons) can be cleaned up by spreading sawdust, cat litter, or another absorbent over the spill. For larger spills (more than 100 gallons), bulldoze soil in front of the spill to prevent it from moving into a waterway. The spill can then be scooped up and spread on land. If accidents occur that result in risks of manure contamination of surface water or groundwater, contact the professionals listed in your emergency plan for help.
Discuss the emergency plan, the location of the emergency phone list, and the expected responses with the entire farm crew. If possible, practice response procedures every year as a training exercise.
Acknowledgments
The author would like to express appreciation for the review and comments made by Matthew Robert, visiting research engineer, agricultural and biological engineering, University of Illinois; John L. Welsh, Extension agent, ANR, Virginia Cooperative Extension Rockingham County Office; Scott Jerrell, Extension agent, ANR, Virginia Cooperative Extension Scott County Office; Mark A. McCann, Extension specialist, animal and poultry sciences, Virginia Tech; and Robert Grisso, Extension specialist, biological systems engineering, Virginia Tech.
Resources
American Society of Agricultural and Biological Engineers. 1992 [revised 2005]. Manure Storage and Safety. ASABE EP470.
Dougherty, Mark, Larry D. Geohring, and Peter Wright. 1998. Liquid Manure Application Systems Design Manual. NRAES-89. Northeast Regional Agricultural Engineering Service.
Field, William E. 1999. Farm Rescue: Responding to Incidents and Emergencies in Agricultural Settings. NRAES-10. Northeast Regional Agricultural Engineering Services and Cooperative Extension.
MidWest Plan Service. 1993. Livestock Waste Facilities Handbook. 3rd ed. MWPS-18. Iowa State University. https://www-mwps.sws.iastate.edu
Natural Resources Conservation Service, Virginia. 2020. Conservation Practice Standard. Nutrient Management. Code 590. https://efotg.sc.egov.usda.gov/api/CPSFile/3950/590_VA_CPS_Nutrient_Management_2020.
Natural Resources Conservation Service, Virginia. 2017. Conservation Practice Standard. Waste Storage Facility (Code 313). https://efotg.sc.egov.usda.gov/api/CPSFile/528/313_VA_CPS_Waste_Storage_Facility_2017.
Natural Resources Conservation Service, Virginia. 2017. Conservation Practice Standard. Nutrient Management. Code 590. https://efotg.sc.egov.usda.gov/api/CPSFile/3950/590_VA_CPS_Nutrient_Management_2020.
Natural Resources Conservation Service, Virginia. 2017. Operation & Maintenance Plan Waste Storage Facility (Code 313). https://efotg.sc.egov.usda.gov/api/CPSFile/530/313_VA_OM_Waste_Storage_Facility_2017.
Other Helpful VCE Publications
Virginia Cooperative Extension. 2024. Selection and Location of Poultry and Livestock Manure Storage. VCE publication 442-307. https://www.pubs.ext.vt.edu/442/442-307/442-307.html.
Virginia Cooperative Extension materials are available for public use, reprint, or citation without further permission, provided the use includes credit to the author and to Virginia Cooperative Extension, Virginia Tech, and Virginia State University.
Virginia Cooperative Extension is a partnership of Virginia Tech, Virginia State University, the U.S. Department of Agriculture (USDA), and local governments, and is an equal opportunity employer. For the full non-discrimination statement, please visit ext.vt.edu/accessibility.
Publication Date
July 24, 2024