Management Tips for Round Bale Hay Harvesting, Moving, and Storage
ID
442-454 (BSE-332P)
Hay production and feeding is one of the most expensive components of forage-livestock systems. Specific management practices are necessary to maintain hay quality and minimize hay loss during harvest, transportation and storage of large round bales.
Large round bale packaging systems allow one person to harvest, store and feed large quantities of hay. Proper management is required to maximize effectiveness because losses during baling, transport and storage of large round bales can far exceed the losses with rectangular bale systems.
Why Consider a Large Round Bale System?
Hay producers select large round balers over small rectangular balers because of their high capacity, lower cost, and lower labor requirements. One person, with properly sized equipment, can usually bale, store and feed all the hay for most average size operations.
When Is a Large Round Bale System a Poor Choice?
Major disadvantages of large round bales include poor long distance transportability, and potential losses from baling, transporting, storage and feeding. Large round bale systems are less suitable than small square bales on steeply sloped fields. These disadvantages can be minimized with proper management.
The round shape and bale dimensions make it impossible to achieve a transport payload equivalent to small or large rectangular bales. Long distance transport of round bales is generally impractical. In addition, there is less demand for large round bales on the open hay market than for small and large rectangular bales. If you plan to sell or transport large round bales, consider a 4-ft-wide round bale that fits better on trucks than wider round bales.
The disadvantage of the 4-ft-wide bales is that they tend to topple over when ejected from the baler. The risk of toppling increases with bale diameter. E.g., a 5-ft-diameter bale is more stable than a 6-ft-diameter bale that is only 4-ft-wide. When toppled bales are left in the field, exposure to rainfall and wicking of soil moisture are intensified. Excessive moisture encourages degradation and heating of the bale, resulting in significant reduction in feed quality.
Bale Shape and Hay Nutritive Value Considerations
Know your hay market and the desired package shape before selecting a haying system.
Dry matter (DM) and crude protein (CP) losses generally are greater with large round bale systems than with small rectangular bale systems, although this generally is of less concern with grass hays. In contrast, shatter losses with legume hays can be particularly costly, as legume leaves often are two to three times greater in CP and digestibility than the stems.
For example, when baling very dry alfalfa hay (less than 15 percent moisture content) leaf losses with large round balers may exceed 25%; such losses seldom exceed 5% with small bales. Because of this potential for loss, timely field operations are more critical with large round bales than with small rectangular bales. Use equipment and management techniques specifically designed for large round bales, since baling, transport, storage and feeding losses of large round bales can be higher than with small rectangular bales.
Selection of Large Round Balers
Most large round balers have a distinct bale chamber within the machine. This chamber will be a fixed (constant size) or variable chamber baler (which adjusts bale size by the amount of hay in the chamber).
Variable chamber balers have flat belts or chains with slats that contain the bale from initial formation until completion. These balers make relatively dense bales that have uniform density from the center out.
In a fixed chamber baler, hay rolls within the chamber until the chamber is filled. These bales tend to have a soft core. The fixed chamber is normally confined by belts, chains, rollers or drums.
Bale chamber losses are less for variable chamber balers with belts than for fixed chamber balers with rollers. However, rollers may require less maintenance than belts or chains.
Large round balers come in a wide range of sizes. The smallest balers produce a full-sized bale approximately 4-ft-wide by 4-ft-diameter. The largest balers make bales nearly 8-ft-wide by 6-ft-diameter. Assuming hay is 15-18% moisture, bale weights vary from 500 to 2,500 lbs in properly conditioned hay. Bale weights will also vary with regard to the type and/or species of forage being baled (e.g., grass vs legume, 1st vs 2nd cutting). Balers with a variable chamber produce uniform density bales in any diameter up to full size. Fixed chamber balers will not produce a maximum density bale until it reaches full size.
Modern large round balers are available with an assortment of options. The choice of package system has important implications for storage, which will be discussed later. Some companies offer a bale monitor system which automatically guides the baler operator across windrows to produce uniformly-shaped bales. Some balers eject the bale and close the tailgate without requiring stopping.
When selecting the various types of bale wrapping system options for your baler, it is important to keep in mind what type of large bale storage you will be utilizing for the majority of your large bales. Things to consider would include, but are not limited to, indoor vs outdoor storage, and “outdoor and covered” vs “outdoor with no cover.”
Some models have been introduced which contain two bale chambers. This arrangement allows a new bale to be started while a full bale is wrapped with twine and ejected, all without stopping forward travel. This will decrease the field capacity of the baling operation especially as yield increases. A bale counter, full bale warning light, and gate-closed indicator are useful options to help improve safety, the quality of the bale, and effectiveness of the balers.
Power required for large round balers varies with the size of baler, size of bale, density of bale formed, rate of bale formation, and contour of the field. As a rule of thumb, the smallest balers require 40 horsepower and the largest balers require at least 100 horsepower.
For safety concerns, the most important thing to consider when matching a tractor to a round baler is not just horsepower but tractor size. It is important that the gross weight of the tractor be greater than that of the gross weight of the fully loaded baler. Tractor weight becomes critical when selecting the proper power unit for a baler that will be used on the hilly slopes.
The cost per hour ($/hr) to operate a round baler is about the same whether the baler is operated at 60% of design capacity (ton/hr throughput) or 90%. Cost per bale is calculated as:

Although it is advantageous to operate the baler at maximum design capacity, this is tempered by site considerations and operator knowledge. For example, driving too fast along heavy windrows can result in a jammed baler, which will require significant time to disentangle. Most balers are equipped with a slip clutch on the pickup mechanism. As the slip clutch is engaged due to overloading, the operator can hear the noise and slow forward progress. Most operators need to keep the baler operating at 90% of design capacity.
Bale Wrapping
Twine tie is available on almost all balers and wrapping materials (twine, net, and plastic). An automatic twine wrap feature speeds wrapping. One has several considerations when comparing twine, net wrap, and plastic wrap. Net or plastic wraps often are preferred by producers in order to reduce outside storage losses. These materials are wrapped around the circumference of the bale in order to increase water shedding and reduce its absorption from the ground.
Wrapping bales with ultraviolet (UV) light-stabilized plastic can reduce DM losses to only 7 percent compared with 35 percent losses from unwrapped bales stored outside on the ground. Solid plastic wrap can be applied at baling when proper attachments are used in combination with late model balers. Wrapping during baling avoids the additional labor needed with bale bonnets or sleeves. No twine is needed with self-adhesive plastic wrap, thereby offsetting a portion of the cost.
Net wraps are porous materials designed to shed water and permit greater air flow at the bale surface at lower cost than plastic wraps. Net wraps are applied during baling and eliminate the need for twine. Net wrap can reduce grass hay DM losses by more than 30 percent when compared with twine-wrapped bales stored outside on the ground. Net wrap is intermediate between plastic and twine in terms of outside storage losses. Net wrapping can make for faster in-field operations. Before ejection from the baler, net wrap requires two spins to wrap the netting compared to eight times required for twine. Reduction in the stop time to wrap a bale offsets the higher cost of the net. Total baling cost per bale for an efficiently run operation is about the same.
Hay Preparation for Large Round Balers
The moisture content of hay entering the baler will greatly influence the amount of field loss and quality of hay after storage. This is generally more critical with a large round baler than with a rectangular baler. In particular, a large round baler will have excessive field loss when the hay is too dry. Generally, harvesting hay during early stages of maturity produces bales that have lower storage losses than late-cut material. Following are management tips to reduce losses and improve quality for the large round bale systems:
Cutting - Hay is usually cut with a sickle-type or disc-type mower, a windrower, or swather. The cutting mechanism must be sharp and properly adjusted to cut the forage cleanly and to minimize shattering. Cutting after the dew is gone and when the topsoil is dry reduces soil compaction and to hasten hay drying. Leave the swath as wide as possible - exposure to sunlight is the primary factor in drying speed. A long stubble keeps the windrow off the soil surface to aid drying and will improve subsequent pickup performance. Leaving a higher stubble height is also important for the long term health of grass stands - mowing too close slows regrowth and encourages weed encroachment. Because disk mowers can cut very close to the ground surface, special shoes may be needed to maintain adequate cutting height.
Disc mowers also allow hay to be cut earlier in the morning or later in the evening, extending the cutting window. Less leaf shattering occurs with increased leaf moisture. Under typical Virginia conditions, it will be best to start mowing in the morning to increase the hours of sunlight exposure. Waiting until evening to harvest can prolong post-harvest respiration (due to lower temperatures and high humidity) and lengthen the curing process, both of which can reduce forage nutritive value.
Conditioning - Plants with an 80 percent moisture content must lose about 6,000 lbs of water per acre to produce a ton of hay at 20 percent moisture. Conditioning speeds drying by opening the waxy cuticle layer surrounding the stem and allowing moisture to evaporate faster. This can be done either mechanically or chemically. Mechanical conditioners pass hay between two rolls to crush or crimp the stem. Avoid flail type conditioners because excessive shatter losses will occur.
Correctly adjusted conditioners maintain adequate roll pressure uniformly along the entire roll length. Apply sufficient roll pressure to the hay to cause a noticeable breaking of the stem skin, but not so much pressure that leaves are broken off. Keep the rolls clean and free of wrapped material. Check to insure that the roll has not worn more in the center than near the ends. A constant diameter roll is necessary to maintain uniform pressure.
Chemicals for conditioning, such as potassium carbonate, partially dissolve the waxy layer and are usually applied by spraying standing legume hay immediately prior to cutting. Both chemical conditioning and mechanical conditioning can be used together. Best results from conditioning occur under favorable drying conditions. Some chemicals used for conditioning also may improve the palatability of the forage.
Tedding - Tedding fluffs, spreads or moves the swath or windrow of hay. All these operations may improve drying, but high leaf loss can occur when the tedder is aggressive or the hay is already somewhat dry when tedded. For alfalfa and clover hay production, hay must be somewhat moist when tedded to reduce leaf shattering. Proper timing of the tedding process for alfalfa and clover will enhance both drying time and forage quality. It is best to ted a few hours (2-4) after the hay is mown. This may require switching from mowing to tedding operations before all the mowing is done.
Windrow turning - Inverters are machines designed to lift, invert and fluff the hay expose the bottom side of the windrow to the sun. During good drying conditions, this will speed the drying. Handling by the turner is about equal to a re-raking with a side-delivery rake. Many consider this a gentler method of handling hay, although the benefit to forage nutritive value may not always justify the added cost.
Raking - Raking forms a mowed swath into a windrow, or accumulates two or more windrows into one. Raking often causes more leaf loss than any other harvest operation. Especially avoid raking legumes when the forage moisture is less than 35 to 40 percent. If the rake is power-take-off (PTO) driven, synchronize field speed and PTO speed to provide a gentle lifting and turning action. This will avoid aggressive handling of the forage and excessive leaf loss. Be sure to set tines above the ground surface. Too close raking damages tines and adds significant amounts of soil to the forage - this can slow drying and reduces forage nutritive value.
Windrow formation - The ideal windrow width for round balers is between one-half and near full width of the baler pickup. This width range aids uniform bale formation within the chamber.
Make windrows as large as possible within the capacity of the baler pickup to minimize baler losses. This reduces contact between hay and the baler pickup mechanism, and reduces the number of bale turns within the chamber. Large windrows may not be compatible with other equipment or with drying strategy, so some compromise usually is necessary.
To form bales of consistent density and shape, make windrows uniform in width and uniform in the amount of hay contained. Minimize the number of windrow ends. Field loss occurs as the bale turns within the bale chamber. Do not create unnecessary bale chamber loss by running the baler when there is no hay feeding into the chamber.
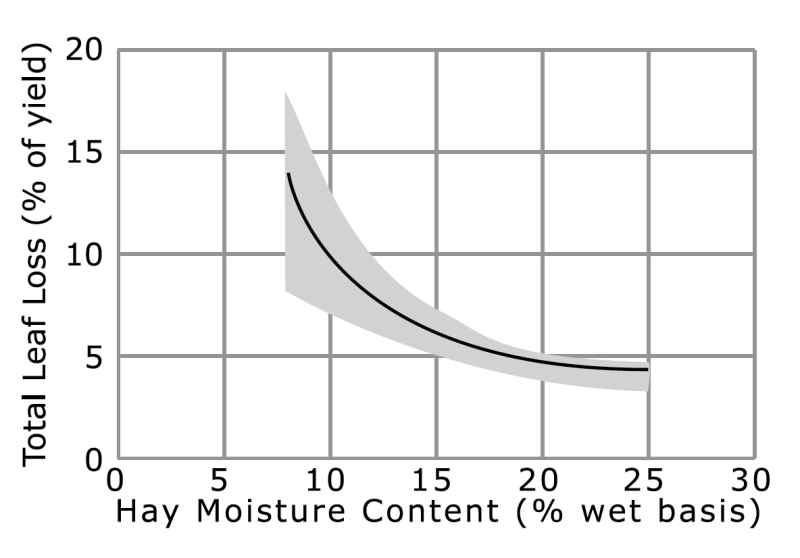
Management Practices to Reduce Baler Losses
Significant DM losses are associated with the entire harvesting process. Total harvest losses, from the standing crop to storage, range as low as 10 percent for grass hay to as high as 35 percent for legumes. More specifically for alfalfa, baling losses of one to five percent have been measured for small rectangular balers operating in typical conditions. Under the same conditions, baling losses with large round balers can range from 3 to 30 percent. Minimize this potentially high loss when using large round balers by controlling losses due to: 1) moisture content of the hay, 2) the baler pickup, and 3) the bale chamber.
Hay moisture content
Hay moisture content is the largest single factor contributing to leaf loss during baling. Figure 1 shows the importance of baling at higher moisture contents. Hay baled at a moisture content above 15 percent has much less leaf loss than hay baled below 15 percent moisture.
The upper moisture level depends on the type of hay, density and size of bale, drying conditions after baling, and other factors. The upper limit for moisture for large round alfalfa bales is typically 18 to 20 percent. Hay baled much above 20 percent moisture will usually spoil unless chemical preservatives such as propionic acid are added to the hay. Effective hay preservatives will prevent excessive heating and mold growth when applied uniformly and at the correct rate.
When the hay becomes too dry and brittle and losses become excessive, stop baling and resume in the evening or morning when the leaf moisture level increases. This dew-moistened hay can be baled at a slightly higher moisture level than when it was drying down because dew moisture in the hay is more easily released during curing than internal moisture.
Baler pickup
The baler pickup mechanism of large round balers may cause losses as high as 12 percent, although losses more typically range from 1 to 3 percent. Field speed, size of windrow, hay moisture content and mechanical condition of the pickup mechanism (broken and bent pickup teeth) influence this loss.
Higher moisture content reduces pickup loss. Synchronizing field speed to pickup rotation speed reduces pickup loss. If forward speed is too slow, the pickup device snatches the hay and pulls the windrow apart as it feeds it. If forward speed is too fast, the hay is “bulldozed” in front of the pick-up mechanism. Proper synchronization of forward speed and pickup rotation speed is achieved when the windrow “flows” into the baler with minimum disruption.
A correct speed match will gently lift the hay from the windrow and not push the hay or pull the hay from the windrow. Heavy windrows reduce pickup loss because the baler operates at a reduced field speed and contact with pickup components is minimized. Do not make windrows so wide that hay is lost at the sides of the baler pickup. Check pickup components regularly for missing or bent tines and to ensure that the windrow is handled gently as it flows into the bale chamber.
Undesirable barrel-shaped bales may occur with narrow windrows when the operator follows a smooth weaving pattern (Figure 2b) or drives straight down the windrow (Figure 2c). For more uniform bales, make sharper turns as shown in Figure 2a. First, crowd material into one side of the pickup for 10-12 seconds; then cross quickly to the other side and crowd material into the opposite side of the pickup for 10-12 seconds. Stay on each side more than 10-12 seconds for lighter crops and less than 10-12 seconds for heavier crops.

Bale chamber
Bale chamber losses as high as 18 percent have been measured with large round balers. Bale chamber losses are normally two or three times higher in a large round baler than a rectangular baler. Windrow size, field speed, hay moisture content, bale rotating speed and wrapping of twine contribute to chamber losses.
To minimize bale chamber losses, the moisture content should be as high as possible, and still allow for safe storage. The feed rate should be as high as possible to minimize the number of turns within the bale chamber. A high feed rate can be attained by using large windrows and high forward speeds. Where windrows are narrow or field speeds must be slow, use a lower PTO speed. This results in fewer revolutions to form a bale. PTO speed must be fast enough relative to field speed to maintain satisfactory pickup performance.
In one study of round balers, bale chamber losses were two percent of yield when the bale was formed in two minutes. When bale forming time was 13 minutes with the same hay, the bale chamber loss was 11 percent of yield.
Since bale chamber losses typically exceed pickup losses, it usually is better to accept some pickup loss by driving faster to reduce the time required to form a bale. When wrapping with twine, do not rotate the bale more times than necessary to secure the twine. The fines, primarily leaves, which fall from the bale chamber during twine wrapping are an indication of the bale chamber loss. These fines contain the highest level of nutrients, so minimizing these losses is important.
Large Round Bale Handling and Transportation
Losses between 1 and 10 percent of yield have been reported when large round bales were moved from field to storage site. Short turnaround time from the baling operation to bale removal from the field will decrease hay waste. Bales moved soon after baling do not begin to lose shape and the various types of wraps, particularly twine, do not deteriorate from UV sunlight exposure. Reduce these losses by spacing twine wraps 6 to 10 inches apart, by making a solid, dense bale with cylindrical form, and by using care in handling the bales.
Round bales can be readily handled by tractor-mounted equipment and special round bale wagons. Tractor front-end loaders can load and move large round bales, but use care to prevent accidents involving tractor tipping or allowing the bale to fall or roll from the loader onto the operator. Single bales can be transported with a pickup. When transporting a large number of bales, single bale handling devices are inefficient. Tractor-powered and self-propelled large round bale loaders and transporters are available for large volume situations.
Long distance transportation of large round bales on public highways is covered by certain highway regulations. These regulations may include the maximum width, height and length of the load, the time of day it can be moved on the highway, and methods of securing the load. According to current state law, the securing device (chain, strap or rope) must be at least 1.5 times stronger than the weight of the load it secures. Consult with the appropriate officials for current regulations on the highways you will travel.
Large Round Bale Storage
Most of the losses that occur during outside storage take place on the bottom of the bales where moisture levels remain highest and air movement is the lowest. There are a number of storage techniques that minimize outdoor storage loss:
Make a dense bale - A dense bale will sag less and have less surface area in contact with the ground. A dense surface layer will shed more precipitation and protect the inner part of the bale from weathering. Bale density is affected by the baling machine, the experience of the operator, and the hay type (fine stemmed hays form denser bales). The density of round bales should be a minimum of 10 lbs of hay per cubic ft.
Use plastic twine, net wrap, plastic wrap, and tarps - Twine reduces bale sag, maintains bale shape, and provides a tight, smooth surface. Plastic twine will resist weathering, insects and rodents better than natural fiber twines. Twine should be tightly wound around the bale at 6 to 10 inches apart for best bale storage. Net wrap or plastic are more effective at shedding and preventing water absorption and would be preferable to twine if outdoor storage is the only option. However, covering bales with high-durability tarps may be an effective, low-cost method of minimizing outdoor storage losses.
Store bales on a well drained location - Bales soak up moisture if placed on a wet or poorly-drained site, causing a large layer of spoiled hay on the bottom of the bale. The storage site should drain away in all directions. A well drained, 4 to 6 inch coarse rock base will minimize bottom spoilage. Other materials that acan be used to prevent soil contact and provide some air space between the bale and soil surface include: telephone poles, wooden pallets, cross ties, scrap pipe and tires.
Store bales end-to-end - The arrangement of large round bales in outdoor storage can significantly influence the amount of storage loss. Pack the bales tight enough to maintain uniform shape and minimize contact with the soil surface. Under most conditions, position bales end-to-end as tightly as possible in long lines on a well drained site. A gently sloping site with a southern or southeasterly exposure is preferable to maximize solar drying and will allow water to quickly drain away from the hay. Bales should be oriented up and down the slope so that they will not create puddling of surface water. Place the bales near the top of the slope to minimize water flowing around the bales. If more than one line of bales is needed, space adjacent lines at least 3 ft apart. This will increase air flow around the bales and allow the sun to reach the back row. Stacking large round bales usually increases losses. Stacking tends to trap moisture and limits drying action from exposure to the sun and wind. Never store bales under trees. It is highly recommended that large bales stacked outside have some type of temporary cover placed over them for the total duration of the storage period.
Large round bales typically have high storage losses when stored outdoors. Remember that the outer 4-inchthick layer of a 6-ft-diameter round bale contains about 25 percent of the total bale volume. Outdoor storage losses range between 5 and 35 percent depending on the amount of precipitation, ambient temperatures, storage site location, original condition of the bale, and time in storage. Placing round bales outside on the ground may seem the cheapest method of hay storage but in reality can be quite expensive given both the losses of DM and declines in forage nutritive value that occur.
Bale Covers, Indoor Storage and Stacking
If bales are to be marketed or stored for more than one season, bale covers or indoor storage are recommended. Storing bales outdoors with good plastic coverings will reduce losses by about half compared with uncovered bales kept outside. Storing bales indoors reduces storage losses by about two thirds compared with outdoor storage.
Care must be taken when storing bales in high stacks. Bales exert significant side forces when stacked high. Be sure the storage structure is capable of withstanding this load. High storage also presents greater risk of injury with hay handling due to changes in the center of gravity if tractors or loaders are undersized for the bales.
Acknowledgments:
The authors acknowledge the contributions of past coauthors, John Cundiff, Don Ohanehi, John Perumpral, and Ray Smith.
Virginia Cooperative Extension materials are available for public use, reprint, or citation without further permission, provided the use includes credit to the author and to Virginia Cooperative Extension, Virginia Tech, and Virginia State University.
Virginia Cooperative Extension is a partnership of Virginia Tech, Virginia State University, the U.S. Department of Agriculture (USDA), and local governments, and is an equal opportunity employer. For the full non-discrimination statement, please visit ext.vt.edu/accessibility.
Publication Date
July 1, 2020