Hydroponic Production of Edible Crops: Nutrient Film Technique (NFT) Systems
ID
SPES-463NP
Introduction
With the increasing number of controlled environment agriculture farms, Virginia Cooperative Extension is working closely with specialty crop growers to address the challenges of establishing and managing hydroponic greenhouse operations. Growers interested in producing food crops in controlled environments can use several different types of hydroponic systems (Resh 2017).
One of the most common types of hydroponic systems is called nutrient film technique (NFT). NFT was first described by Dr. Allen Cooper in his book, ABC of NFT (1980), based on his work at the Glasshouse Crops Research Institute in Littlehampton, England in the 1960s. NFT is an active, recirculating system where plants are grown in channels (Figure 1). A thin film of nutrient solution is pumped through these channels to provide water and fertilizer to the roots of the plants. This publication will give an overview of NFT systems and will include descriptions and images of standard set-ups. Growers should consider there are many variations on the main components listed here.

Set-Up and Design
NFT systems are scalable and can be constructed of different materials however the major components are similar (Figure 2). All NFT systems have a bench/table support structure, nutrient solution reservoir, plant growing channels, collection components and nutrient delivery components. In a well-designed NFT system, the movement of nutrient solution is from the reservoir via pumping action to the plant channels where the solution flows past the exposed roots by gravity to the collection system. The collection system then returns the solution to the reservoir where it is again pumped to the plants. This constitutes the circular flow of nutrient solution in the system.

Table/Bench Support System
The solution feed system, plant channels and drain system all must be supported above the nutrient solution reservoir. This is one of the first components to be constructed and designed for the NFT system. It can be made from various materials including square or round metal tubing, wood, masonry blocks, etc. This table/bench can be made at any height convenient for planting and harvest but
should be high enough and sloped enough to allow for drainage of the nutrient solution back into the reservoir. Growers should consider making this support structure strong enough so that the plant channels don’t warp or bend under weight and heat (Figure 3).

Nutrient Reservoir
The reservoir is some type of container that holds the nutrient solution. It is positioned at the lowest point in the system as all solution flows back to the reservoir by gravity. A plastic container is most often used as a metal container could react with the fertilizer solution and cause corrosion of the container. Some growers use plastic garbage containers, buckets, plastic totes, poly tanks, IBCs, and plastic livestock watering troughs (Figure 4).

The size of the reservoir is determined by the number of plants to be grown in the system. As a general rule, ¼ to 1 gallon of capacity per plant in the container is adequate. For example, a 50-plant system might have a reservoir with a 25 gallon capacity. One consideration for the grower is to oversize reservoir volume in the system to better buffer against pH and nutrient changes. Overall, reservoir selection should be based on availability, price and size of the system the grower is designing.
Irrigation Input
The start of the movement of nutrient solution from the reservoir is with the pump. In most small systems a submersible pump is used inside the reservoir while larger systems typically rely on a pool-type centrifugal pump (Figure 5).

Regardless of the pump type, it should be rated for continuous duty and be sized with enough head pressure to overcome delivery height and friction loss to deliver solution to the plant channels. The flow rate from the pump should be 3 to 5 gallons per hour into each channel. Growers should consider having a backup pump available in case of pump failure. The pump is attached to a plumbing system that is usually PVC solid piping or another type of poly piping that is rated for the pressure of the pump output. This usually consists of a header or manifold pipe that is connected to the plant channels through smaller delivery tubing (Figure 6).

Both the manifold piping and delivery tubing should be a flexible material. The connection between the manifold and delivery tubing is with an emitter.
These emitters can be direct flow through or pressure compensating and inserted directly into the flexible poly pipe (Figure 7).
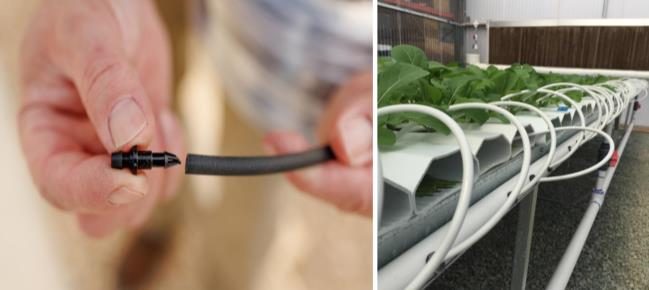
Shut-off valves can be added to the delivery lines or manifolds to adjust flow rates of soulution into the plant channels. Growers in different climates should consider choosing the proper color poly pipe as white tubing reflects heat and keeps the nutrient solution cooler while black tubing has the opposite effect.
Plant Channels
The plant channels hold the plant from the seedling stage through harvest. These channels are sometimes called “trays” or “gutters” and can be made from different materials but plastic material is the most widely used. Generally, channels are made from PVC plumbing pipe as well as commercially available PVC molded units (Figure 8). Plumbing pipe is used mostly by hobbyist or small-scale growers and is usually 2 inch schedule 40 pipe. Growers use a drill bit or hole saw to make plant spaces in the pipe. Spacing for most leafy green crops in these systems is 8 inches on center.

Commercial channels can be purchased from vendors that have plant spaces preinstalled. These channels are flat on the bottom surface and range in width but are usually 4 inches wide and 1½ inches to 2 inches deep. Some channels have removable top caps and most have end caps. For either type of plant channel, length can vary from 4 feet to 12 feet (Figure 9). Growers should consider shape, cost and dimensions when purchasing plant channels.

Solution Collection
Nutrient solution flows in the channels past the plant roots and is returned to the nutrient reservoir. The collection system usually consists of a larger lighter drainage pipe that the channels feed into. Insertion holes can be drilled into this collection pipe but should be slightly oversized to allow for easy removal and insertion of the channels (Figure 10).

If necessary, nutrient solution could be processed through a filter before returning to the reservoir or directly return without filtration. Growers should consider constructing a stable attachment or base for this collection pipe as it can contain more weight per length than the channels.
Crops
Occasionally fruiting crops such as strawberries, peppers, tomatoes, and cucumbers are grown in these systems. However most often crops grown in NFT systems are low-growing, leafy greens and culinary herbs. Various types of lettuce work very well in an NFT system such as butterhead, romaine, oakleaf, multi-leaf. Other salad greens like sorrel, arugula, tatsoi, mache, and frisee also work well in this type of system (Figure 11).

Many of these plant types have different colors and textures which can work well in bagged leafy green mixes. Cultivars that are adapted to greenhouse conditions can be found from seed vendors. Growers should consider market value/need, plant habit, maturity date, and resistance to disease and physiological problems when selecting plant types and cultivars.
Propagation is from seed and usually occurs in a separate area from the main system after which the seedlings are placed in the NFT channels. Raw seed is used in some cases but very commonly pelleted seeds (raw seeds coated with an inert material to yield a consistent size and shape) are used. Seedlings planted into an NFT system are most times produced by seeding into media made of materials like Rockwool, foam, or compressed peat/coir. These materials come as a cube that is sized to fit into the NFT channels and also have a dimpled depression on the top to accommodate a seed (Figure 12).

All of these types of media hold moisture well and allow for uniform germination. In the seedling area after germination seedlings are given partial strength nutrient solution as the germination media adds no nutrients to the plants.
Nutrient Solution Management
Nutrient solution can be made by mixing fertilizers with water in the reservoir. Water soluble powdered fertilizers and liquid premixed fertilizers are most often used (Figure 13). Fertilizer mixing instructions are given by fertilizer suppliers based on the crop being grown and are on the fertilizer packaging.

Growers should consider a fertilizer program that provides all the necessary macro and micro elements needed for optimum growth. One nutrient solution example would be to provide all the needed nutrients to the plants by using a complete fertilizer such as 8-15-36 along with calcium nitrate and magnesium sulfate. These fertilizers, mixed in the correct amounts based on the labeling instructions for the volume of water in the reservoir, should be mixed separately and then added to the reservoir. After the addition of the fertilizer and agitation of the tank, the pump can be turned on to provide nutrient solution to the system.
Water quality meters are necessary to the management of the nutrient solution in the NFT system including meters for electrical conductivity (EC), pH, and dissolved oxygen (DO) (Figure 14).

Meters vary in price and quality. Growers should consider meter longevity, reliability, price and accuracy when purchasing. Electric conductivity (EC) and pH should be checked two to three times each week. EC measurement lets the grower know if the total amount of fertilizer in solution has changed over time. Adjustment of fertilizer strength, based on the EC reading, of the solution can be made through the addition of stock fertilizer solution or water.
Many leafy greens perform well at EC 1.2 to 2.0 mS/cm. The pH measurement lets the grower know about the acidic or basic nature of the solution, which can affect nutrient uptake by the plants. Most plants grown in these systems perform well at pH 5.5 to 6.2.
Conclusion
Nutrient film technique (NFT) hydroponic systems can vary in size, complexity, and makeup. However, this type of production systems can be a great way to grow crops. This publication gives a general overview of NFT, however potential growers should investigate specific options for their unique situation. Growers should consider contacting their local Cooperative Extension office for more information.
References
Cooper, A. 1980. ABC of NFT: Nutrient Film Technique: The World's First Method of Crop Production Without a Solid Rooting Medium. International Specialized Book Services, Inc.
Resh, H. 2017. Hydroponic Food Production. CRC Press. 7th Edition.
Additional Resources
Cornell College of Agriculture and Life Science https://cea.cals.cornell.edu/
North Carolina State University https://cals.ncsu.edu/horticultural-science/research/greenhouse-vegetable-production/
Ohio State University https://u.osu.edu/greenhouse/hydroponic-crop-program-introduction/
Pennsylvania State Extension https://extension.psu.edu/hydroponics-systems-and-principles-of-plant-nutrition-essential-nutrients-function-deficiency-and-excess
Sallenave, R. and R. C. Shultz. 2022. Hydroponics: Water-saving Farming for New Mexico's Arid Environment. New Mexico State University Cooperative Extension Service.
University of Arizona https://ceac.arizona.edu/
Acknowledgements
This work was supported by the Virginia Department of Agriculture and Consumer Services (VDACS) Specialty Crop Block Grant Program, Award Number 2020-548, from the U.S. Department of Agriculture’s (USDA) Agricultural Marketing Service. Any opinions, findings, conclusions, or recommendations expressed in this publication are those of the authors and do not necessarily reflect the view of the US. Department of Agriculture.
Virginia Cooperative Extension materials are available for public use, reprint, or citation without further permission, provided the use includes credit to the author and to Virginia Cooperative Extension, Virginia Tech, and Virginia State University.
Virginia Cooperative Extension is a partnership of Virginia Tech, Virginia State University, the U.S. Department of Agriculture (USDA), and local governments, and is an equal opportunity employer. For the full non-discrimination statement, please visit ext.vt.edu/accessibility.
Publication Date
July 24, 2023